Research and development
CHARTING A PATH OF
INNOVATION IN OUR DESIGNS
Our products are fully designed and developed in-house.
Our engineering department, R&D team, and quality department form an interdisciplinary group of over 40 professionals, designers and engineers. With expertise in materials, structures, thermal engineering, vibrations, corrosion and automation, they work closely with clients to develop custom solutions and tackle the most demanding challenges. Careful performance monitoring in marine environments worldwide drive our continuous innovation and improvement.
IDEAS, INSIGHTS, CONCEPTS
In developing our products, we start by analysing the client’s specific requirements, anticipated load levels, and classification society standards. Drawing on our extensive experience in the naval field, we proactively address potential issues on board, enabling us to develop effective and tailored solutions.
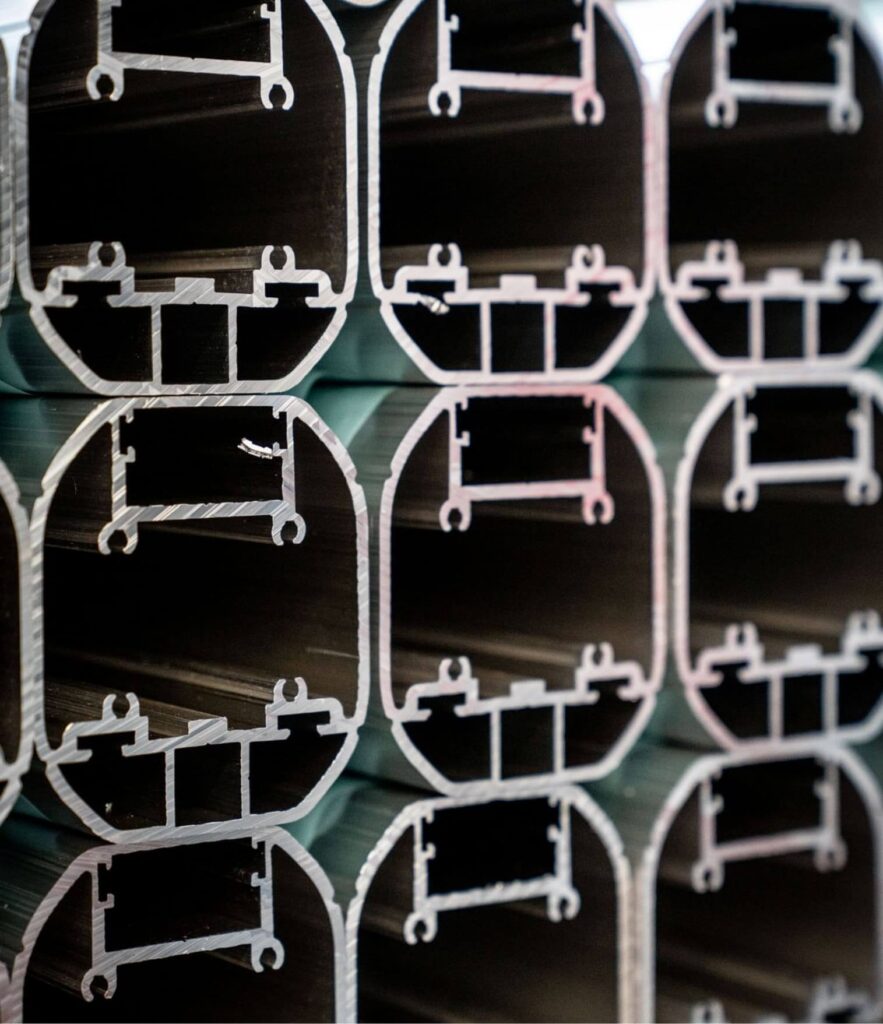
ENGINEERING
Our products must withstand extremely high pressures and this requires rigorous structural tests. We utilise 3D modelling and Finite Element Analysis (FEA), validated by classification societies, to ensure regulatory compliance.
For products with thermal insulation requirements, we conduct dedicated tests. For projects with unique specifications, we develop 1:1 scale prototypes, subjecting them to dynamic tests for glazed walls, balustrades and windscreens, as well as static load tests for other applications.

3D PRINTING, PROTOTYPES, MOCKUPS
We use cutting-edge 3D printers to create prototypes and accessories. Our wire-based printer produces robust models in fibreglass-reinforced resin, while our stereolithography (SLA) printer crafts high-precision components in rigid plastic or soft rubber. These technologies enable us to conduct preliminary evaluations, both visual and structural. The R&D department then works in tandem with the engineering department to develop full-size mockups, giving clients a realistic, life-size representation of the products that will be installed on board.
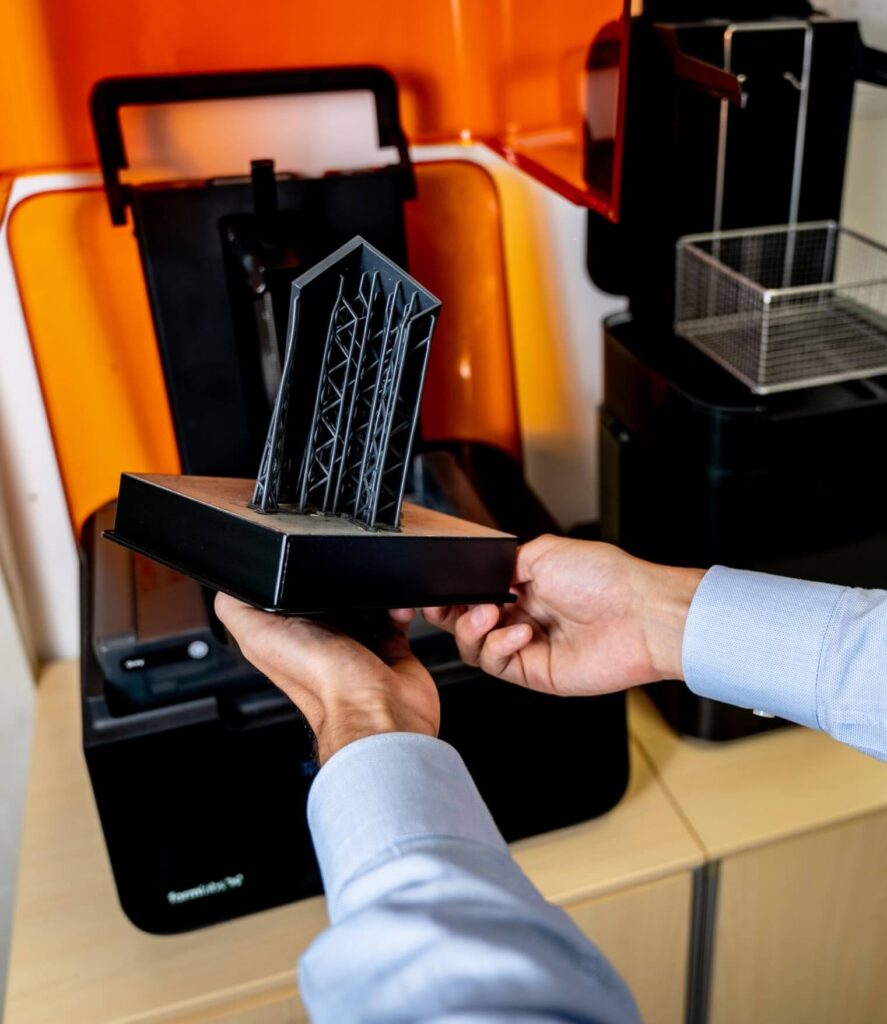
IN-HOUSE LABS FOR ANALYSIS AND TESTING
Our in-house labs perform rigorous and advanced tests, including water, air and wind tests, environmental chamber tests, and salt spray tests, along with structural and impact resistance assessments. With the support of external partners, we then develop dies, seals and accessories, culminating in the construction of the pilot run prototype for official validation and certification testing. Additionally, we design fire resistant systems that adhere to MED regulations and are certified in accredited labs.
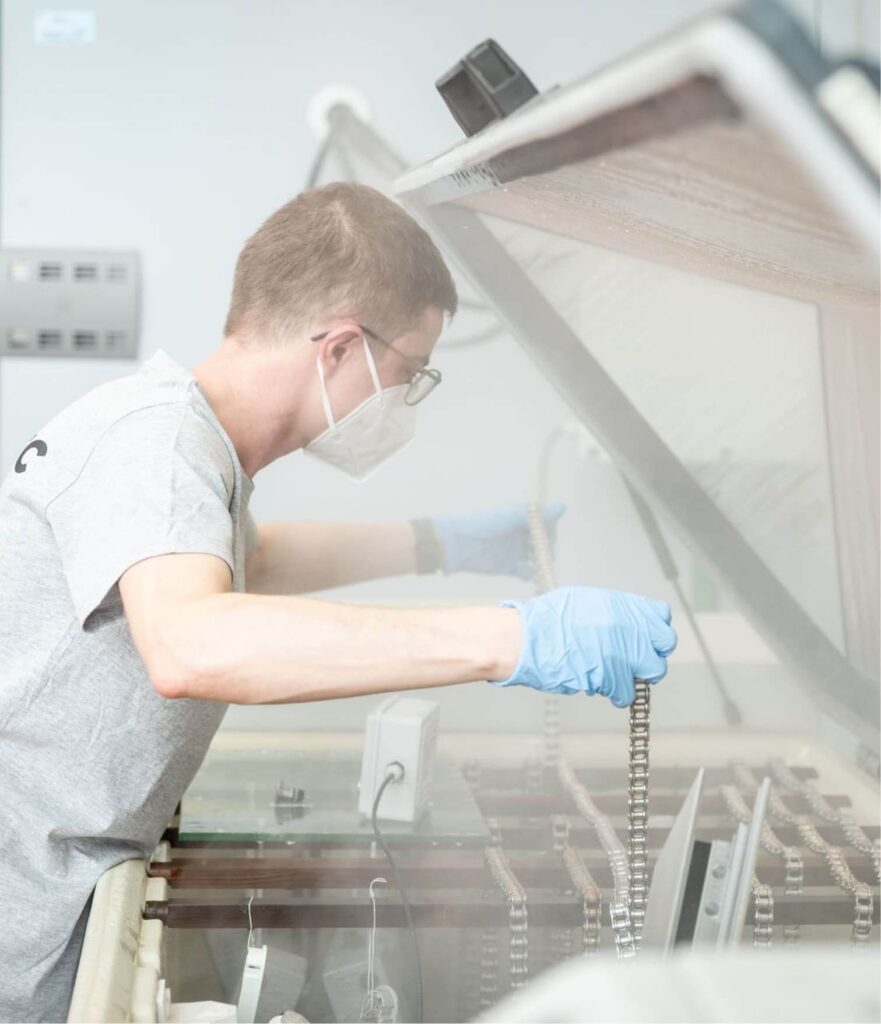
INDUSTRIALISATION AND CERTIFICATIONS
Taking a product from idea to market demands a thorough, structured process. After in-house testing, our next steps are certification and industrialisation. Certification is crucial to ensure compliance with naval standards and involves technical assessments by external bodies that validate the performance results obtained in our labs. Once certified, the prototypes are transitioned into industrial processes that retain their design characteristics in large-scale production. Departments work in close coordination to ensure a smooth transition from lab to production line, guaranteeing the highest quality and meeting deadlines.
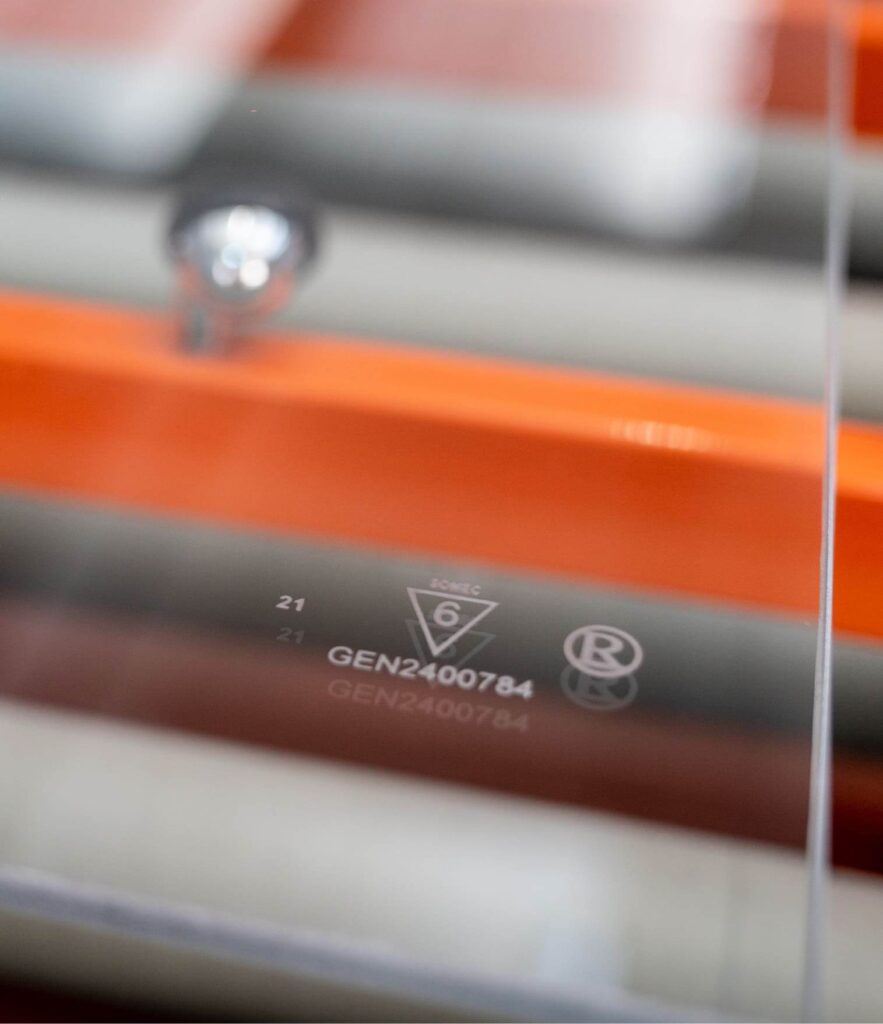
SHOWROOM AND MOCKUP AREA
Our showroom offers an immersive experience, letting you see our products in a realistic setting. Visitors can explore a wide range of installed solutions as if they were actually on the ship. The exhibition space is an important part of our R&D Lab, connecting the testing and prototyping area within its 400 sqm space. The showroom is a meeting place for clients and partners and showcases our integrated approach: every product on display is the result of a cycle that combines innovation, experimentation and industrialisation.
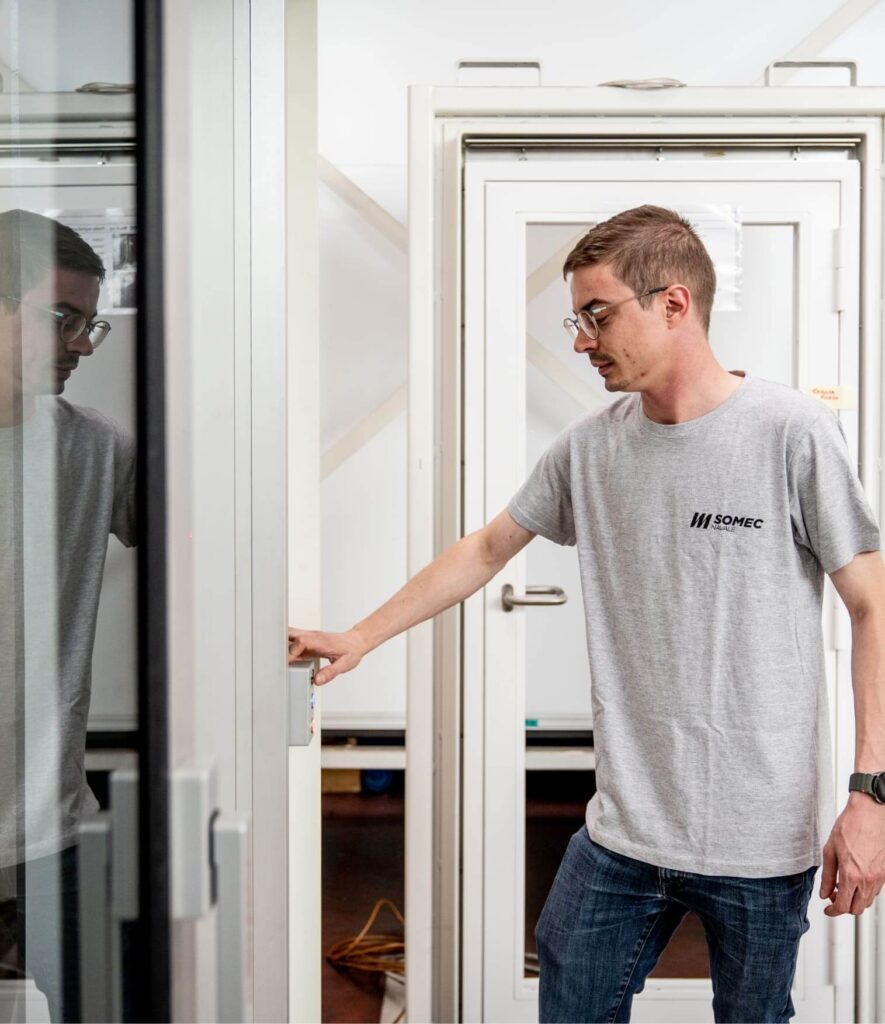